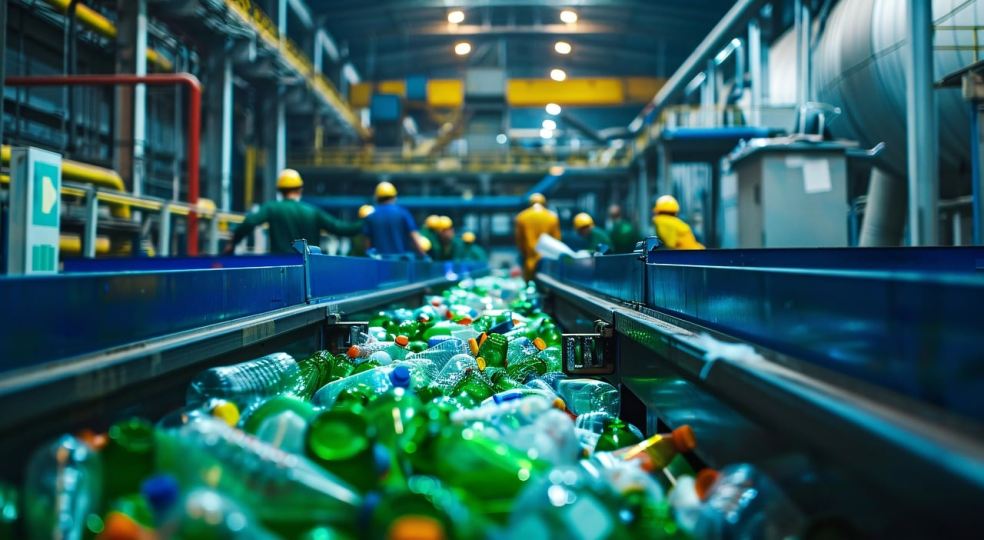
The plastics industry is entering a new era shaped by digitalisation and the rise of smart factories
The plastics industry plays a crucial role in the global economy, creating and providing a wide range of products and services that are used extensively across many other industries, such as construction, electronics, automotive, healthcare, aviation, transportation, manufacturing, and so on. Plastic has become a ubiquitous material in our modern times, being part of our daily lives and produced in larger quantities each year, and despite controversies regarding its negative impact on the environment, its utility cannot be denied.
Therefore, it’s not a surprise that the plastic sector is thriving, with a global production volume of 400.3 Mt and a market size estimated at 712bn USD in 2023. It’s also natural that the industry is constantly advancing, taking big strides towards a new era in its evolution. Like many other areas of activity, the plastics industry is experiencing major changes that will impact and transform key practices and aspects related to production, processing, and distribution. So, let’s take a closer look at the factors driving these changes and how they are going to shape the future of the industry.
Integration of advanced technologies
Digital transformation has swept across all industries in recent decades, revolutionising the way they conduct their operations, and the plastics industry makes no exception. Various cutting-edge technologies are currently employed in the sector, and many others will likely be introduced in the future, with the purpose of increasing efficiency, ensuring sustainability and compliance, and streamlining the entire production process. Out of all the digital solutions that plastic manufacturers have embraced, the following three are making the most notable difference.
Internet of Things (IoT)
The Internet of Things, or IoT in short, refers to a network of physical devices that are connected over the Internet, collecting and sharing information with each other to help users track and manage different variables and make more informed decisions. The plastics industry can leverage IoT capabilities to monitor and control machinery and systems, ensuring an optimal production environment. For example, the success of the injection moulding process for large plastic products relies on precision, so embedding production equipment with IoT sensors can help manufacturers like HSV TMP adjust parameters in real-time to reduce inconsistency and thus produce items that meet high-quality standards.
The constant connectivity that IoT provides can also help with predictive maintenance. The performance data that IoT sensors collect from different components is used to detect anomalies or signs that indicate potential issues and determine when machines require repairs or maintenance work. This can help companies avoid major breakdowns and reduce downtime considerably.
Artificial Intelligence (AI)
Artificial intelligence is the driving force behind the transformation of many domains. In plastics production, AI is primarily used to facilitate quality control and ensure that the products that come off the production line meet the highest standards. With the assistance of AI-based tools, manufacturers can optimise testing processes and detect defects and issues with greater accuracy, allowing them to take immediate action when necessary. This not only reduces the risk of human error but also improves brand reputation and assists with regulatory compliance.
Big Data Analytics
Plastic manufacturers, like many other businesses and organisations, also deal with large volumes of data, many of them collected via IoT systems, which makes drawing actionable insights a rather cumbersome endeavour. Here’s where big data analytics comes into play, helping manufacturers process the information they’ve gathered and identify trends, patterns, and other valuable insights that they can use to address specific challenges and issues, such as preventing production bottlenecks, optimising the thermoplastic injection moulding process, or reducing waste.
The emergence of smart factories
Thanks to tech advances and the introduction of digital solutions, traditional manufacturing plants are now giving way to smart factories, where devices and processes are interconnected, and new solutions are employed to address longstanding challenges. The rise of smart factories in the plastics industry brings numerous advantages, as follows:
- Improved efficiency and productivity – automated systems and flexible processes allow smart factories are able to overcome former limitations and create more efficient workflows. This makes it easier for manufacturers to improve productivity levels and adapt to changing market demands.
- Better visibility – smart factories understand that their success is highly dependent on how they manage their supply chain. Therefore, they take advantage of innovative tech solutions to gain better visibility into their supply chains and stay on top of every stage, from sourcing to production to distribution. Having a bird’s eye view of the supply chain also ensures faster response times and consistent performance.
- Sustainability – due to rising environmental concerns, sustainability has become an imperative nowadays for businesses in all industries, and plastics is one of the most targeted sectors due to its high pollution rates. Through the use of AI, data analytics, IoT, and other advanced technologies, smart manufacturing factories are able to minimise their carbon footprint and comply with current standards around environmental protection.
New regulations
Another notable change set to reshape the sector is the introduction of new regulations that aim to address the thorny plastic pollution issue that has been hanging over the industry like a black cloud for years. For example, the new rules adopted by the EU Parliament in 2024 have set packaging reduction targets of 5% by 2030, 10% by 2035, and 15% by 2040. To reach these objectives, manufacturers, and importers will have to reduce the weight and volume of plastic packaging. Newly adopted measures also specify that certain types of single-use plastic packaging will be banned starting January 2030.
All these initiatives and trends are bound to bring notable improvements to the plastic industry and lead it toward a new era of prosperity where tech innovations and sustainability take center stage.