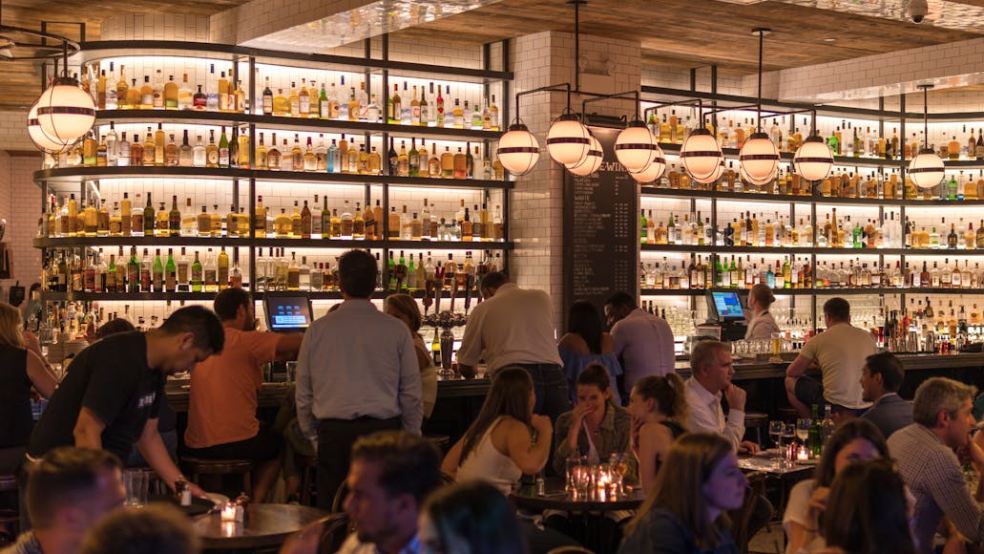
Preventive Maintenance Planning: Creating a Schedule That Protects Your Hospitality Investment
In the fast-paced hospitality industry, equipment downtime can rapidly escalate from a minor inconvenience to a significant financial crisis. A malfunctioning air conditioning system during peak summer, refrigeration failure in a busy kitchen, or electrical issues affecting guest rooms can damage your reputation and bottom line. At EnviroFWA, we've witnessed how proper preventive maintenance planning can transform operations from reactive crisis management to proactive efficiency.
Whilst many hospitality businesses understand the importance of maintenance, creating a structured, comprehensive schedule requires specialised knowledge. This article will guide you through developing an effective preventive maintenance plan that protects your investment, reduces operational disruptions, and extends the lifespan of your critical systems.
The True Cost of Maintenance Neglect in Hospitality
Before exploring preventive strategies, it's essential to understand what's at stake. Research indicates that reactive maintenance typically costs 3-9 times more than planned maintenance approaches. For hospitality businesses, the costs extend beyond immediate repairs:
- Revenue loss from service disruptions or room unavailability
- Reputation damage through negative guest reviews
- Increased energy consumption from inefficiently operating equipment
- Premature equipment replacement costs
- Staff productivity losses when dealing with emergency situations
- Compliance risks related to safety and health regulations
Our experience with Envirofwa planned and reactive maintenance has shown that businesses implementing comprehensive preventive strategies typically reduce their total maintenance costs by 12-18% annually, whilst experiencing fewer disruptions.
Building Your Preventive Maintenance Framework
A successful preventive maintenance programme requires a structured framework comprising several interconnected elements:
1. Asset Inventory and Criticality Assessment
The foundation of effective maintenance planning is a comprehensive inventory of all maintainable assets. This should include:
- Equipment identification with make, model and serial numbers
- Installation dates and expected service life
- Maintenance history and documentation
- Manufacturer's recommended service schedules
- Location and accessibility information
- Criticality rating (how essential the equipment is to operations)
Critical systems like air conditioning, refrigeration, and primary electrical systems should receive priority attention in your maintenance schedule, as their failure would have the most significant operational impact.
2. Seasonal Priorities for Hospitality Businesses
The hospitality industry experiences distinct seasonal patterns that should influence maintenance scheduling:
Winter Maintenance Priorities
- Heating system comprehensive service
- Building envelope inspection for heat loss
- Pipe insulation verification to prevent freezing
- Snow and ice management system review
- Holiday season emergency response planning
Spring Maintenance Priorities
- Air conditioning system preparation
- Ventilation system cleaning and verification
- Exterior building maintenance
- Cooling tower cleaning and treatment
- Pest control measures implementation
Summer Maintenance Priorities
- Refrigeration system performance optimisation
- Cooling system peak efficiency maintenance
- Water system legionella risk assessment
- High-demand wear component inspection
- Backup power system testing
Autumn Maintenance Priorities
- Heating system preparation
- Ventilation system rebalancing for the heating season
- Building weatherisation
- Emergency lighting and fire safety system verification
- Plumbing system winter preparation
Our TM44 inspection service ensures your air conditioning systems are evaluated and optimised before peak cooling demand seasons arrive.
For more details, click here.
3. Regulatory Compliance Integration
Hospitality businesses must navigate numerous regulatory requirements related to equipment maintenance. An effective preventive maintenance schedule should incorporate all legally required inspections, including:
- Fire safety systems - including fire damper drop testing
- Emergency lighting - with our fire alarm and emergency lighting services
- Electrical safety - through fixed wire testing and portable appliance testing
- Water safety - via legionella risk assessment and water sampling
- Ventilation hygiene - through TR19 grease extraction, cleaning and certification
- Refrigeration safety - especially for systems using regulated refrigerants
Integrating these requirements into your preventive maintenance schedule ensures compliance whilst optimising service visits and minimising disruption.
4. Maintenance Task Classification and Scheduling
Different equipment requires different maintenance approaches. Your schedule should classify tasks by type:
Time-Based Maintenance
Regular servicing based on calendar intervals, such as quarterly air conditioning inspections or annual electrical safety checks.
Usage-Based Maintenance
Maintenance triggered by operating hours or cycles, particularly for high-use equipment like kitchen refrigeration or laundry systems.
Condition-Based Maintenance
Using monitoring to determine when maintenance is required, such as vibration analysis on ventilation fans or thermal imaging of electrical systems.
Predictive Maintenance
Utilising data analysis to forecast when failures might occur and intervening before they happen—increasingly important for sophisticated building management systems.
Our planned maintenance services can help you determine the most appropriate maintenance strategy for each system.
5. Resource Allocation and Budgeting
Effective preventive maintenance requires appropriate resource allocation:
- Financial resources - typically 2-4% of asset replacement value annually
- Staffing requirements - internal maintenance team capacity planning
- Specialist contractor scheduling - for systems requiring certified technicians
- Parts and materials inventory - for commonly required components
- Tools and equipment - necessary for regular maintenance tasks
Balancing in-house capabilities with specialist contractor services like those offered by EnviroFWA can optimise your maintenance budget whilst ensuring all systems receive appropriate attention.
Digital Maintenance Management: Modern Solutions for Complex Schedules
Manual tracking of complex maintenance schedules across multiple systems and locations is increasingly impractical. Modern Computerised Maintenance Management Systems (CMMS) offer significant advantages:
CMMS Capabilities for Hospitality Businesses
- Automated scheduling of preventive maintenance tasks
- Mobile access for technicians to access documentation on-site
- Real-time reporting of maintenance status and history
- Inventory management for spare parts and materials
- Work order generation and tracking
- Compliance documentation storage and retrieval
- Cost tracking across equipment and maintenance types
- Performance analytics to identify trends and opportunities
When implementing a CMMS, ensure it integrates with your property management system to minimise guest disruption when scheduling maintenance activities.
Staff Roles and Responsibilities in Maintenance Planning
A clear definition of maintenance responsibilities is essential for programme success:
Management Responsibilities
- Establishing maintenance policies and standards
- Allocating sufficient resources and budget
- Reviewing maintenance performance metrics
- Ensuring regulatory compliance
- Making equipment replacement decisions
Maintenance Staff Responsibilities
- Executing scheduled maintenance tasks
- Documenting work performed
- Identifying potential issues beyond the scope
- Maintaining parts inventory
- Providing technical feedback on equipment performance
Operational Staff Responsibilities
- Reporting equipment issues promptly
- Following proper equipment operation procedures
- Performing basic daily maintenance checks
- Coordinating maintenance access to spaces
- Understanding emergency procedures
Our technical teams work collaboratively with your staff to ensure clear communication and responsibility assignment when implementing maintenance programmes.
Risk Assessment and Prioritisation Techniques
Not all equipment failures present equal risk. A formal risk assessment process helps prioritise maintenance activities:
Risk Evaluation Matrix
- Identify potential failure modes for each system
- Assess the probability of each failure occurring
- Determine the severity of the consequences if failure occurs
- Calculate risk score (probability × severity)
- Prioritise maintenance based on the highest risk scores
This approach ensures critical systems like commercial refrigeration or air conditioning receive appropriate priority in resource allocation.
Documentation and Record-Keeping Best Practices
Comprehensive documentation is vital for maintenance continuity and compliance:
Essential Maintenance Documentation
- Equipment specifications and manufacturer guidance
- Standard operating procedures for maintenance tasks
- Completed maintenance records with technician details
- Repair history including parts replaced
- Test certificates and compliance documentation
- Warranty information and service contracts
- Equipment performance data and efficiency metrics
Digital record-keeping systems significantly improve accessibility and searchability of maintenance documentation, particularly important during regulatory inspections or emergency situations.
Case Study: The Riverside Hotel Belfast
A 120-room hotel in Belfast was experiencing frequent disruptions from equipment failures and rising maintenance costs. After implementing a comprehensive preventive maintenance schedule with EnviroFWA's guidance:
- Emergency repair calls decreased by 68% in the first year
- Energy consumption reduced by 14% through improved equipment efficiency
- Guest complaint incidents related to environmental comfort fell by 42%
- Overall maintenance costs decreased by 23% despite increased planned maintenance activity
- Staff time spent managing maintenance issues reduced by 35%
The hotel's investment in preventive maintenance planning achieved full return within 16 months while significantly improving guest experience metrics.
Special Considerations for Listed or Historic Hospitality Properties
If your hospitality business operates in a listed or historic building, preventive maintenance planning requires additional considerations:
- Heritage-compatible solutions that preserve architectural features
- Specialised contractors with experience in historic buildings
- Alternative approaches for areas where standard access is limited
- Seasonal sensitivity to minimise impact on building fabric
- Enhanced documentation of unique building characteristics
- Coordination with conservation authorities, where applicable
Our experience with historic properties ensures maintenance can be performed effectively whilst respecting architectural significance.
Implementing Your Preventive Maintenance Schedule
Once developed, successful implementation of your maintenance schedule requires:
1. Phased Introduction
Begin with critical systems and gradually expand to comprehensive coverage.
2. Staff Training
Ensure all relevant personnel understand their roles in the maintenance programme.
3. Regular Review Cycles
Establish quarterly reviews to assess programme effectiveness and adjust as needed.
4. Continuous Improvement Process
Use maintenance data to refine and optimise the schedule over time.
5. Contractor Coordination
Develop clear communication protocols with specialist maintenance providers like EnviroFWA.
The Strategic Value of Preventive Maintenance
A well-designed preventive maintenance schedule represents a strategic investment in your hospitality business rather than simply an operational cost. By shifting from reactive to preventive approaches, you'll not only reduce direct maintenance expenses but also enhance:
- Guest satisfaction through reliable, comfortable environments
- Staff productivity by minimising disruptions
- Asset longevity and performance
- Property value through well-maintained systems
- Operational predictability and budget control
- Compliance with evolving regulations
At EnviroFWA, our comprehensive understanding of hospitality maintenance requirements allows us to support you in developing and implementing effective preventive maintenance schedules tailored to your specific property. From ventilation hygiene cleaning to water tank maintenance and refrigeration services, our integrated approach ensures all your critical systems receive appropriate attention.
Contact us today to discuss how a customised preventive maintenance schedule could transform your hospitality operation from reactive crisis management to proactive efficiency.