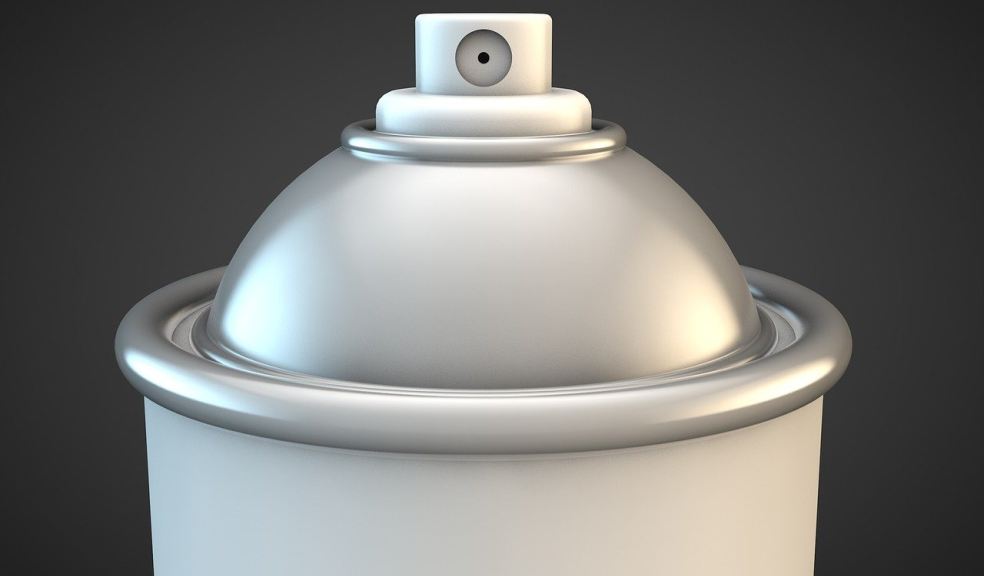
Step-by-Step Breakdown of the Bag On Valve Aerosol Filling Process
The Bag-On-Valve (BOV) aerosol market, valued at $11.8 billion in 2024, is anticipated to grow significantly, reaching $21.37 billion by 2031. This robust growth reflects a substantial compound annual growth rate (CAGR) of 8.85% from 2024 to 2031, showcasing the expanding demand and application of BOV systems in various industries. The increase in market value highlights the rising preference for efficient and environmentally friendly aerosol packaging solutions.【source】
As the BOV market continues to expand, understanding the intricate details of the Bag-On-Valve aerosol filling process becomes crucial. This guide provides a step-by-step breakdown of the BOV filling process, highlighting key stages from placement and pressurization to sealing and testing. By examining these steps, we gain insight into how BOV systems ensure product integrity and efficiency, which are pivotal to meeting the growing market demands.
Step 1: Place the B.O.V. Inside the Container
The first step in the B.O.V. filling process involves inserting the Bag On Valve assembly into the aerosol container. The B.O.V. consists of a flexible, laminated bag attached to a valve, allowing for the separation of the product from the propellant. This separation is crucial for maintaining the purity and stability of the product. The bag is carefully placed inside the container, ensuring it is properly positioned to prevent any kinks or folds that could interfere with the dispensing mechanism. This initial step sets the foundation for the entire process, as the proper placement of the B.O.V. is essential for efficient and consistent product delivery.
Step 2: Add Pressure to the Container
Once the B.O.V. is securely positioned, the next step is to introduce pressure into the container. This is achieved by filling the space outside the bag with a propellant gas, such as compressed air or nitrogen. The choice of propellant depends on the product's requirements and the desired spray characteristics. The propellant is introduced through a valve, and the amount of pressure is carefully controlled to achieve optimal levels. This pressurization is essential for the B.O.V. system to function correctly, as it creates the necessary force to expel the product from the bag when the valve is activated.
Step 3: Crimp and Seal the B.O.V. to the Container
After pressurizing the container, the valve must be crimped and sealed to the container's opening. This step involves using specialized crimping equipment to secure the valve assembly, creating an airtight seal. The crimping process is critical for maintaining the container's internal pressure and preventing any leakage of the propellant gas or the product. A precise and secure seal is necessary to ensure the longevity and reliability of the aerosol system. Any imperfections in the seal could lead to pressure loss or contamination, compromising the product's quality and safety.
Step 4: Fill the B.O.V. with the Product Through the Valve
Following the sealing of the valve, the product is filled into the bag through the valve. This step requires meticulous control to ensure the correct dosage and avoid overfilling. The B.O.V. system's design allows for the product to be introduced without coming into contact with the propellant, preserving its integrity. This feature is particularly beneficial for products sensitive to contamination or degradation when mixed with propellants. The filling process can accommodate various product consistencies, from liquids to creams, making it versatile for different applications. The filling is done with precision to ensure that the right amount of product is dispensed with each use.
Step 5: Conduct a Water Bath Test to Ensure There Are No Leaks
To verify the integrity of the sealed container, a water bath test is performed. This quality assurance step involves submerging the filled and sealed containers in a water bath and observing for any bubbles, which would indicate leaks. The water bath test is a standard procedure in the aerosol industry, providing a reliable method to detect any potential flaws in the sealing process. Ensuring that there are no leaks is crucial for maintaining the product's shelf life and safety. This test confirms that the container can retain its internal pressure and protect the product from external contamination.
Step 6: Attach the Actuator and Place the Cap on the Container
The final step in the B.O.V. aerosol filling process is attaching the actuator and placing the cap on the container. The actuator, or spray nozzle, is fitted onto the valve stem and is designed to control the release and spray pattern of the product. The actuator must be securely attached to ensure consistent and reliable dispensing. Once the actuator is in place, a protective cap is added. The cap serves multiple functions: it protects the actuator from damage, prevents accidental discharge, and keeps the nozzle clean. This final assembly step ensures the product is ready for packaging and distribution.
The Bag On Valve aerosol filling process is a sophisticated and highly controlled procedure that offers numerous benefits over traditional aerosol systems. By keeping the product separate from the propellant and ensuring precise filling and sealing, the B.O.V. system provides superior product stability and safety. This comprehensive guide to the B.O.V. process outlines the critical steps involved, highlighting the attention to detail and quality control measures required to produce a high-quality aerosol product. As a result, the B.O.V. system is an ideal choice for a wide range of products, offering consumers a reliable and convenient packaging solution.
Conclusion
This article explores Bag on Valve (BOV) systems. As a leading manufacturer in the BOV industry, we offer a variety of empty BOV containers, including sizes of 30ml, 50ml, 80ml, 100ml, 150ml, 180ml, 300ml, and 500ml. Additionally, we provide complete sets of aluminum cans and actuators. For those needing filling services, we offer OEM options and can either use our existing formulas or develop new ones tailored to your specifications.
Our company utilizes an advanced Automatic Production Line to ensure both efficiency and consistency in manufacturing. We perform a comprehensive 24-hour BOV leak test to guarantee the highest standards of quality, complying with FDA and LFGB regulations. Our products are produced in a GMP-certified workshop, ensuring a safe and hygienic production environment. With 20 years of experience in BOV production and a 30-day delivery timeframe, we invite you to contact us for detailed information on our Bag on Valve packaging solutions.